How Can You Effectively Remove Moisture From an Air Compressor?
When it comes to maintaining an air compressor, one common challenge that many users face is the buildup of moisture within the system. Moisture can lead to a host of problems, from corrosion and rust to reduced efficiency and potential damage to tools and equipment. Understanding how to remove moisture from an air compressor is essential for prolonging its lifespan and ensuring optimal performance.
Air compressors naturally draw in air from the environment, which often contains varying levels of humidity. As the air is compressed, the moisture condenses and accumulates inside the tank and piping. Without proper management, this trapped moisture can cause significant issues, including contamination of pneumatic tools and compromised air quality. Addressing this moisture effectively is a crucial step in routine compressor maintenance.
In the following sections, we will explore the importance of moisture removal, common signs that indicate excessive moisture buildup, and the practical methods and tools available to keep your air compressor dry and functioning at its best. Whether you’re a seasoned professional or a DIY enthusiast, gaining insight into moisture control will help you protect your investment and maintain reliable operation.
Common Methods to Remove Moisture From Air Compressors
Moisture accumulation in air compressors can lead to corrosion, reduced efficiency, and damage to pneumatic tools. Removing this moisture effectively requires understanding the available methods and their applications. Several approaches are commonly used to manage and eliminate moisture from compressed air systems.
One straightforward method is the use of drain valves. These valves are typically installed at the bottom of air receiver tanks or after filters to allow accumulated water to be expelled manually or automatically. Regular draining prevents water buildup and prolongs equipment life.
Another effective method is the installation of air dryers, which come in various types designed to reduce moisture content:
- Refrigerated Air Dryers: These cool the compressed air to condense water vapor, which is then removed by a drain. They are suitable for general industrial use where dew points around 35°F (2°C) are acceptable.
- Desiccant Air Dryers: These use moisture-absorbing materials (desiccants) to adsorb water vapor, achieving much lower dew points, often below -40°F (-40°C). They are ideal for applications requiring very dry air.
- Membrane Air Dryers: These rely on selective permeable membranes to separate moisture from the air stream, usually for smaller systems or portable units.
Installing aftercoolers is another practical option. Aftercoolers reduce the temperature of compressed air immediately after compression, causing moisture to condense out. This condensed water is then removed via drains.
Maintaining and Monitoring Moisture Removal Systems
Proper maintenance of moisture removal equipment ensures optimal performance and longevity. Regular inspection and cleaning of drain valves prevent clogging and malfunction. For automatic drains, periodic testing confirms they operate correctly, avoiding unnecessary air loss or water accumulation.
Air dryer desiccant material must be replaced or regenerated based on manufacturer guidelines. Failure to maintain desiccant integrity diminishes drying efficiency and allows moisture to pass through the system.
Monitoring moisture levels in compressed air is essential for early detection of problems. This can be achieved through:
- Dew Point Meters: Measure the temperature at which moisture condenses from the air.
- Moisture Indicators: Visual devices installed in air lines to detect the presence of water.
- Pressure Gauges and Flow Sensors: Help identify blockages or leaks that may cause moisture issues.
Comparison of Moisture Removal Techniques
Different moisture removal methods suit various operational needs, costs, and maintenance requirements. The following table summarizes key aspects to help determine the appropriate solution for your air compressor system.
Method | Operating Principle | Typical Dew Point | Maintenance | Best Use Case |
---|---|---|---|---|
Drain Valves (Manual/Automatic) | Expel accumulated condensate | Dependent on system temperature | Regular inspection and cleaning | General moisture removal from tanks |
Refrigerated Air Dryer | Cool air to condense moisture | ~35°F (2°C) | Periodic cleaning of heat exchangers | Industrial plants with moderate moisture control |
Desiccant Air Dryer | Adsorb moisture using desiccants | As low as -40°F (-40°C) | Replace or regenerate desiccant regularly | Critical applications needing very dry air |
Membrane Air Dryer | Selective moisture permeation through membranes | Variable, moderate dew points | Replace membranes as needed | Portable or small-scale systems |
Aftercoolers | Cool compressed air to condense moisture | Dependent on cooling capacity | Regular cleaning and drain maintenance | Preliminary moisture removal after compression |
Understanding the Sources of Moisture in Air Compressors
Moisture accumulation in air compressors primarily arises from the condensation of water vapor present in the intake air. When ambient air is compressed, its temperature rises, but as the compressed air cools down in the system, water vapor condenses into liquid form. This moisture can cause corrosion, reduce the efficiency of pneumatic tools, and contaminate finished products, making moisture control critical.
Key factors contributing to moisture presence include:
- Ambient humidity: Higher humidity levels increase the amount of water vapor entering the compressor.
- Temperature fluctuations: Cooling of compressed air results in condensation.
- Compressor design: Some compressors generate more heat or have less efficient moisture separation capabilities.
Effective Methods to Remove Moisture from Air Compressors
Removing moisture involves a combination of mechanical devices and maintenance practices designed to separate and drain water from compressed air systems. Implementing these methods ensures dry, clean air for optimal compressor performance.
Method | Description | Advantages | Considerations |
---|---|---|---|
Air Dryer | Devices that remove moisture from compressed air before it enters the system, including refrigerated and desiccant dryers. |
|
|
Aftercoolers | Heat exchangers that cool compressed air, causing moisture to condense for easier removal. |
|
|
Drain Valves and Traps | Automatic or manual valves that periodically remove accumulated condensate from tanks and pipelines. |
|
|
Moisture Separators | Internal components that use centrifugal force or filters to separate moisture from compressed air. |
|
|
Routine Maintenance Practices to Minimize Moisture Buildup
Consistent maintenance is essential to ensure moisture does not accumulate and degrade air compressor performance. Key practices include:
- Regularly drain condensate: Check and empty drain valves, tanks, and filters to prevent water pooling.
- Inspect and clean air filters: Clogged filters can increase pressure and cause moisture retention.
- Monitor and service air dryers: Replace desiccant material or service refrigerated dryers as recommended.
- Check piping and connections: Ensure no leaks or blockages that could trap moisture.
- Maintain optimal operating temperature: Avoid excessive cooling that promotes condensation in the system.
Additional Tips for Reducing Moisture in Compressed Air Systems
Beyond mechanical solutions and maintenance, consider the following strategies to further reduce moisture content:
- Use intake air filters with moisture removal capabilities: These can reduce water vapor entering the compressor.
- Locate compressors in dry, temperature-controlled environments: This limits moisture ingress from ambient air.
- Implement proper pipe insulation: Prevents condensation inside air lines due to temperature differences.
- Employ pressure dew point monitoring: Allows real-time tracking of moisture levels for timely intervention.
Expert Strategies for Removing Moisture From Air Compressors
Dr. Emily Chen (Mechanical Engineer, Compressed Air Systems Specialist). Proper moisture removal begins with understanding the source of condensation within the compressor system. Installing refrigerated or desiccant air dryers downstream of the compressor effectively reduces moisture content, preventing corrosion and extending equipment lifespan. Regular maintenance of drain valves and moisture traps is also critical to ensure optimal performance.
James Patel (Industrial Maintenance Manager, Precision Manufacturing Inc.). In my experience, the most reliable method to remove moisture from air compressors is the integration of automatic condensate drains combined with high-efficiency filtration. These systems continuously expel accumulated water without manual intervention, which minimizes downtime and protects pneumatic tools from water damage.
Sophia Martinez (Compressed Air Quality Consultant, AirTech Solutions). To effectively manage moisture in compressed air, I recommend a multi-stage approach: first, cool the compressed air to condense moisture, then use a coalescing filter to capture fine water droplets, and finally, employ a desiccant dryer for critical applications requiring ultra-dry air. This layered strategy ensures maximum moisture removal tailored to specific industrial needs.
Frequently Asked Questions (FAQs)
What causes moisture buildup in an air compressor?
Moisture accumulates due to condensation when compressed air cools inside the tank and piping. Ambient humidity and temperature fluctuations also contribute to this buildup.
How can I effectively remove moisture from an air compressor?
Use a combination of methods such as installing a moisture separator, draining the tank regularly, and employing refrigerated or desiccant air dryers to remove water vapor from the compressed air.
How often should I drain the moisture from my air compressor tank?
Drain the tank daily or after each use in humid environments to prevent water accumulation and corrosion. Automatic drains can simplify this maintenance.
What type of air dryer is best for removing moisture from compressed air?
Refrigerated air dryers are suitable for most applications, removing bulk moisture efficiently. For extremely dry air requirements, desiccant dryers provide superior moisture removal.
Can moisture damage my air compressor or tools?
Yes, moisture can cause internal corrosion, reduce compressor efficiency, and damage pneumatic tools by causing rust and impairing lubrication.
Is it necessary to use filters along with moisture removal systems?
Yes, filters help remove oil, dirt, and residual moisture, ensuring clean and dry air, which prolongs equipment life and maintains optimal performance.
Effectively removing moisture from an air compressor is essential to maintain its performance, extend its lifespan, and ensure the quality of compressed air. Moisture accumulation can lead to corrosion, damage to pneumatic tools, and compromised end products. Common methods for moisture removal include using air dryers such as refrigerated or desiccant dryers, installing moisture separators and filters, and regularly draining the compressor tank to expel accumulated water.
Understanding the source and impact of moisture in compressed air systems allows operators to select the most appropriate moisture control solutions tailored to their specific applications. Routine maintenance practices, including timely draining and inspection of moisture removal components, are critical in preventing moisture-related issues. Additionally, integrating multiple moisture control methods can provide enhanced protection and reliability.
In summary, proactive moisture management in air compressors not only safeguards equipment but also improves operational efficiency and product quality. By implementing proper moisture removal techniques and adhering to maintenance schedules, users can ensure optimal compressor functionality and reduce the risk of costly repairs or downtime.
Author Profile
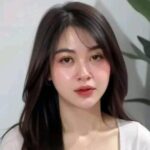
-
Tamika Rice is a lifestyle journalist and wellness researcher with a passion for honest, relatable storytelling. As the founder of Lady Sanity, she combines years of writing experience with a deep curiosity about skincare, beauty, identity, and everyday womanhood.
Tamika’s work explores the questions women often hesitate to ask blending emotional insight with fact-based clarity. Her goal is to make routines feel empowering, not overwhelming. Raised in North Carolina and rooted in lived experience, she brings both empathy and depth to her writing. Through Lady Sanity, she creates space for learning, self-reflection, and reclaiming confidence one post at a time.
Latest entries
- July 4, 2025Skincare & Acne CareCan I Use Body Sunscreen on My Face Safely?
- July 4, 2025Nail Care & BeautyHow Long Does a French Manicure Really Last?
- July 4, 2025Makeup & CosmeticsWhy Should You Never Go to the Cosmetics Counter Without Me?
- July 4, 2025Female Empowerment & IdentityHow Many Females Were On Board the Ship Ann?