How Can You Effectively Test Concrete Moisture Levels?
When it comes to working with concrete—whether for flooring, coatings, or structural purposes—understanding its moisture content is crucial. Excess moisture within concrete can lead to a host of problems, from surface bubbling and adhesive failures to long-term structural damage. Knowing how to accurately test concrete moisture ensures that you can make informed decisions, avoid costly mistakes, and achieve durable, high-quality results.
Testing concrete moisture isn’t just for professionals; it’s a vital step for anyone involved in construction, renovation, or maintenance projects. Moisture levels can vary depending on factors like curing time, environmental conditions, and the concrete mix itself. Without proper testing, you risk applying finishes or adhesives over a damp substrate, which can compromise the integrity of your work.
In the following sections, we’ll explore the various methods and tools available to assess concrete moisture effectively. Whether you’re a contractor, DIY enthusiast, or inspector, gaining a solid understanding of how to test concrete moisture will empower you to tackle your projects with confidence and precision.
Common Methods for Testing Concrete Moisture
Several techniques are used to test the moisture content in concrete, each with its own advantages and limitations. Choosing the appropriate method depends on the project requirements, the concrete’s age and condition, and the level of accuracy needed.
One widely used method is the Calcium Chloride Moisture Test, which measures the moisture vapor emission rate (MVER) from the concrete surface. This test is non-destructive and involves placing a small dish of anhydrous calcium chloride on the concrete, sealing it under a plastic dome, and measuring the moisture collected after 60 to 72 hours. It helps predict whether floor coverings can be installed safely.
Another common method is the Relative Humidity (RH) Probe Test, which involves drilling holes into the concrete slab and inserting probes to measure internal humidity levels. This method provides a direct measurement of moisture within the slab and is considered more accurate for assessing the potential for moisture-related floor failures.
The Electrical Resistance Meter or Moisture Meter uses probes to measure the electrical conductivity of the concrete surface, which correlates with moisture content. These meters provide quick, on-site readings but are less accurate and often used for initial assessments.
Additionally, Infrared Thermography can detect moisture-related temperature differences on the concrete surface, highlighting areas with potential moisture issues without physical contact. This method is useful for large areas but requires specialized equipment and interpretation.
Step-by-Step Procedure for Calcium Chloride Moisture Test
Performing a calcium chloride test involves careful preparation and precise execution to ensure reliable results:
- Surface Preparation: Clean the concrete surface thoroughly, removing dust, coatings, adhesives, and any debris. The surface must be dry and smooth.
- Seal the Test Area: Place the calcium chloride test kit on the surface and seal it with a plastic dome or vapor barrier tape to prevent external moisture interference.
- Duration: Leave the test undisturbed for 60 to 72 hours to allow moisture vapor to be absorbed by the calcium chloride.
- Measurement: After the specified time, weigh the calcium chloride packet to determine how much moisture it has absorbed.
- Calculation: Convert the weight gain to moisture vapor emission rate (MVER), usually expressed in pounds per 1,000 square feet per 24 hours (lb/1000 ft²/24 hr).
Interpreting Moisture Test Results
Understanding test data is crucial for making informed decisions regarding concrete flooring or coatings. The following table summarizes typical moisture emission rates and recommended actions:
Moisture Vapor Emission Rate (lb/1000 ft²/24 hr) | Assessment | Recommended Action |
---|---|---|
0 – 3 | Low moisture level | Suitable for most floor coverings |
3.1 – 5 | Moderate moisture level | Use moisture mitigation systems before installation |
5.1 – 7 | High moisture level | Postpone floor covering installation; implement drying measures |
>7 | Excessive moisture | Do not install floor coverings; consult a specialist |
For RH probe tests, relative humidity values below 75% generally indicate safe moisture levels for most flooring systems. Values between 75% and 85% suggest caution and the possible need for mitigation, whereas levels above 85% often require remedial action before proceeding.
Factors Affecting Moisture Test Accuracy
Several variables can influence the reliability of moisture testing results and should be controlled or accounted for during the testing process:
- Concrete Age: New concrete releases more moisture; testing should ideally occur after the concrete has cured sufficiently.
- Surface Conditions: Contaminants or coatings on the surface can affect moisture readings.
- Environmental Factors: Ambient temperature and humidity levels during testing impact moisture movement.
- Test Duration: Insufficient test duration may lead to underestimating moisture emission.
- Concrete Thickness and Composition: Thicker slabs or concrete with additives may retain moisture longer.
Proper calibration of instruments and adherence to standardized testing protocols mitigate inaccuracies and improve data reliability.
Using Moisture Test Results to Guide Flooring Installation
The primary goal of testing concrete moisture is to prevent flooring failures caused by trapped moisture. Flooring materials such as hardwood, vinyl, and adhesives are sensitive to moisture levels. Based on test outcomes, contractors can:
- Select appropriate moisture barriers or sealers.
- Choose moisture-tolerant adhesives and flooring products.
- Adjust installation timing to allow additional drying.
- Implement mechanical drying methods such as dehumidification.
- Consult manufacturer guidelines that specify moisture limits for products.
By integrating moisture testing into project planning, stakeholders reduce risk, enhance floor durability, and ensure compliance with industry standards.
Understanding the Importance of Concrete Moisture Testing
Concrete moisture testing is critical before applying floor coverings, coatings, or sealants to ensure durability and prevent failures such as mold growth, adhesive breakdown, or surface deterioration. Moisture trapped within concrete slabs can cause significant issues if not properly identified and managed.
Several factors affect concrete moisture levels:
- Age of the concrete: Newer slabs typically contain more moisture.
- Environmental conditions: Humidity, temperature, and ventilation influence drying rates.
- Concrete mix and thickness: Variations can affect moisture retention.
- Sub-slab moisture sources: Groundwater or vapor transmission can add moisture.
Understanding these variables helps determine the most accurate testing method and appropriate moisture limits for the project.
Common Methods to Test Concrete Moisture
Several standardized methods exist to assess moisture content in concrete. Each method provides different information and is suitable for different stages or requirements.
Testing Method | Purpose | Procedure | Advantages | Limitations |
---|---|---|---|---|
Calcium Chloride Test (ASTM F1869) | Measures moisture vapor emission rate (MVER) | Place a sealed dish of calcium chloride on concrete surface for 60-72 hours and measure weight gain | Widely accepted, standardized, and directly relates to vapor emission | Surface sensitive, requires several days, affected by surface conditions |
Relative Humidity Probe (ASTM F2170) | Measures internal relative humidity within concrete slab | Drill hole into slab, insert probe, and measure RH after equilibrium | Provides in-situ moisture profile, faster results, less surface effect | Requires drilling, may need multiple readings at various depths |
Moisture Meter (Pin or Pinless) | Quick qualitative surface moisture indication | Use electronic meter on surface or shallow depth | Fast, non-destructive | Not quantitative, affected by surface finish and temperature |
Plastic Sheet Test (ASTM D4263) | Qualitative indication of moisture vapor emission | Tape plastic sheet on concrete for 16-24 hours and observe condensation | Simple, low-cost | Non-quantitative, subjective interpretation |
Step-by-Step Procedure for Conducting a Calcium Chloride Test
The calcium chloride test remains a widely accepted method for assessing moisture vapor emission from concrete slabs. The procedure includes:
- Prepare the Surface: Clean the concrete surface of dust, dirt, and debris. The area should be dry and smooth.
- Select Test Locations: Identify multiple representative spots on the slab, especially in areas prone to moisture issues.
- Seal Test Area: Attach the test chamber or dish securely using a vapor-impermeable adhesive or tape to prevent external air infiltration.
- Place Calcium Chloride: Weigh and place a specified amount of calcium chloride inside the dish according to the manufacturer’s instructions.
- Seal and Wait: Cover the dish and leave it undisturbed for 60 to 72 hours at a stable temperature.
- Weigh and Calculate: After the test period, weigh the dish again to determine the moisture absorbed by the calcium chloride.
- Calculate MVER: Use the weight difference and surface area to calculate the moisture vapor emission rate, typically expressed in pounds per 1,000 square feet per 24 hours (lbs/1000 ft²/24 hr).
Interpreting Test Results and Moisture Limits
Different flooring systems and sealants require specific moisture limits to ensure proper adhesion and performance. Typical accepted moisture vapor emission rates are:
Flooring Type | Maximum Moisture Vapor Emission Rate (lbs/1000 ft²/24 hr) |
---|---|
Vinyl Flooring | 3 |
Epoxy Coatings | 3 |
Carpet with Adhesive | 3 |
Wood Flooring (Engineered or Solid) | 1.5 – 3 (depending on product) |
For relative humidity testing inside slabs, acceptable limits typically range from 75% RH or lower, depending on manufacturer requirements. Exceeding moisture limits necessitates drying, remediation, or use of specialized moisture mitigation systems
Expert Perspectives on How To Test Concrete Moisture
Dr. Emily Carter (Concrete Materials Scientist, National Institute of Building Sciences). Testing concrete moisture accurately begins with understanding the concrete’s age and composition. I recommend using a calcium chloride moisture test for slab-on-grade floors, as it quantifies moisture vapor emission rates effectively. Additionally, non-destructive methods like relative humidity probes embedded within the slab provide ongoing monitoring, which is critical before installing moisture-sensitive flooring.
Michael Tran (Construction Quality Control Manager, BuildRight Solutions). From a practical standpoint, surface moisture tests such as the plastic sheet method can offer quick preliminary insights but are not definitive. For reliable results, we rely on in-situ relative humidity testing combined with moisture meters calibrated for concrete. These tools help us ensure the slab meets industry standards before proceeding with finishes, preventing costly failures related to moisture.
Sara Delgado (Structural Engineer and Concrete Durability Specialist, Advanced Engineering Consultants). It is essential to select the appropriate moisture testing method based on the project’s timeline and environmental conditions. For example, electrical resistance meters provide rapid readings but can be influenced by surface contaminants. Therefore, embedding sensors within the concrete to measure internal moisture levels offers the most accurate assessment of drying progress and potential risks for coating or adhesive applications.
Frequently Asked Questions (FAQs)
What are the common methods to test concrete moisture?
The most common methods include the calcium chloride test, relative humidity (RH) probe test, and the use of moisture meters such as pin-type and pinless meters. Each method measures moisture content differently and suits specific applications.
How does the calcium chloride test work for concrete moisture?
The calcium chloride test measures the moisture vapor emission rate (MVER) from the concrete surface. A sealed dish containing calcium chloride is placed on the slab, and moisture absorption is measured over 60 to 72 hours to assess vapor emission levels.
When is it appropriate to use relative humidity probes inside concrete?
Relative humidity probes are embedded within the concrete slab to measure internal moisture levels. This method is appropriate for new slabs and provides accurate data on moisture conditions that affect flooring installations.
Can moisture meters provide reliable results on concrete slabs?
Moisture meters offer quick, non-destructive readings but may only indicate surface moisture. For comprehensive assessment, they should be used in conjunction with other standardized tests like calcium chloride or RH probe tests.
Why is testing concrete moisture important before flooring installation?
Excess moisture in concrete can cause adhesive failures, mold growth, and flooring damage. Testing ensures moisture levels are within acceptable limits, preventing costly repairs and ensuring the longevity of the flooring system.
How long should concrete cure before moisture testing?
Concrete typically requires a curing period of at least 28 days before accurate moisture testing. Testing too early may result in elevated moisture readings due to residual curing moisture.
Testing concrete moisture is a critical step in ensuring the durability and performance of concrete installations, particularly before applying flooring, coatings, or sealants. Various methods such as the calcium chloride test, relative humidity probe test, and electrical resistance meters offer reliable means to assess moisture levels within concrete slabs. Selecting the appropriate testing method depends on factors like the concrete’s age, thickness, and the specific requirements of the project.
Accurate moisture testing helps prevent common issues such as adhesive failures, mold growth, and surface deterioration, which can result from excessive moisture content. Understanding and interpreting test results correctly allows professionals to make informed decisions regarding moisture mitigation strategies, curing times, and readiness for subsequent construction phases.
Ultimately, implementing a thorough concrete moisture testing protocol contributes to the longevity and success of construction projects. Adhering to industry standards and employing best practices in moisture measurement ensures that concrete surfaces meet the necessary conditions for optimal performance and reduces the risk of costly repairs or failures down the line.
Author Profile
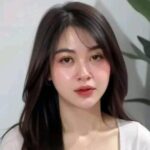
-
Tamika Rice is a lifestyle journalist and wellness researcher with a passion for honest, relatable storytelling. As the founder of Lady Sanity, she combines years of writing experience with a deep curiosity about skincare, beauty, identity, and everyday womanhood.
Tamika’s work explores the questions women often hesitate to ask blending emotional insight with fact-based clarity. Her goal is to make routines feel empowering, not overwhelming. Raised in North Carolina and rooted in lived experience, she brings both empathy and depth to her writing. Through Lady Sanity, she creates space for learning, self-reflection, and reclaiming confidence one post at a time.
Latest entries
- July 4, 2025Skincare & Acne CareCan I Use Body Sunscreen on My Face Safely?
- July 4, 2025Nail Care & BeautyHow Long Does a French Manicure Really Last?
- July 4, 2025Makeup & CosmeticsWhy Should You Never Go to the Cosmetics Counter Without Me?
- July 4, 2025Female Empowerment & IdentityHow Many Females Were On Board the Ship Ann?