How Can You Effectively Remove Moisture From Compressed Air?
Compressed air is a vital resource used across countless industries, powering everything from pneumatic tools to manufacturing processes. However, one common challenge that can compromise the efficiency and longevity of compressed air systems is the presence of moisture. Moisture in compressed air not only reduces performance but can also lead to corrosion, equipment damage, and product contamination. Understanding how to effectively remove moisture from compressed air is essential for maintaining system reliability and ensuring optimal operation.
Moisture enters compressed air systems primarily through the intake of ambient air, which contains varying levels of humidity. When air is compressed, the water vapor condenses, creating liquid water that can accumulate within pipes, valves, and tools. This unwanted moisture can cause rust, clog filters, and even freeze in colder environments, leading to costly downtime and repairs. Addressing this issue requires a strategic approach to drying and moisture removal tailored to the specific needs of the application.
In the following sections, we will explore the fundamental principles behind moisture formation in compressed air and discuss the various methods and technologies available to remove it. Whether you’re managing a small workshop or a large industrial facility, gaining insight into effective moisture control will help you protect your equipment, improve air quality, and enhance overall system performance.
Types of Air Dryers for Removing Moisture
Compressed air systems often incorporate air dryers to efficiently reduce moisture content. Selecting the appropriate type depends on factors such as desired dew point, operating conditions, and budget. Common air dryer types include:
- Refrigerated Dryers: These use refrigeration to cool the compressed air, condensing moisture which is then removed. They typically achieve a dew point of 35°F to 50°F and are suitable for general industrial applications.
- Desiccant Dryers: Utilizing moisture-absorbing materials such as silica gel or activated alumina, desiccant dryers can achieve very low dew points (down to -40°F or lower), ideal for sensitive instrumentation or pneumatic tools.
- Membrane Dryers: These employ selective membranes that allow water vapor to pass through while retaining compressed air, useful for point-of-use drying with moderate flow rates.
- Deliquescent Dryers: Using hygroscopic salts that absorb moisture and dissolve, these dryers are simple and low-cost but require regular maintenance and disposal of the resultant liquid.
Each dryer type offers distinct advantages and limitations, often summarized in operational parameters such as pressure drop, maintenance needs, and energy consumption.
Additional Moisture Removal Techniques
Beyond air dryers, several supplemental methods enhance moisture removal from compressed air systems:
- Aftercoolers: Installed immediately downstream of the compressor, aftercoolers reduce air temperature, causing moisture to condense and be separated. They improve the efficiency of subsequent drying equipment.
- Moisture Separators: Cyclonic or centrifugal separators remove bulk liquid water from compressed air by spinning the air to force droplets to the vessel walls.
- Filters and Coalescers: These trap fine water aerosols and oil droplets, improving air quality and protecting pneumatic equipment.
- Proper Drainage Systems: Automatic or manual drains eliminate accumulated condensate from pipes and tanks, preventing moisture carryover.
Combining these methods with air dryers often results in the most reliable moisture control.
Comparative Performance of Moisture Removal Methods
The table below compares key features of common moisture removal solutions used in compressed air systems:
Moisture Removal Method | Dew Point Range | Typical Pressure Drop | Maintenance Requirements | Energy Usage | Best Applications |
---|---|---|---|---|---|
Refrigerated Dryer | 35°F to 50°F (2°C to 10°C) | Low (1-3 psi) | Moderate (cleaning coils, refrigerant checks) | Moderate | General industrial use, food processing |
Desiccant Dryer | -40°F to -100°F (-40°C to -73°C) | Moderate to High (5-15 psi) | High (periodic media replacement/regeneration) | High (heated or blower regeneration) | Pharmaceuticals, electronics, instrumentation |
Membrane Dryer | 20°F to 50°F (-7°C to 10°C) | Low to Moderate | Low (replace membranes periodically) | Low | Point-of-use, low flow rates |
Deliquescent Dryer | 30°F to 50°F (-1°C to 10°C) | Minimal | Moderate (media replacement) | None | Portable systems, low-cost applications |
Aftercooler + Moisture Separator | Condensate removal only | Low | Low (periodic drain checks) | Minimal | Pre-treatment for dryers, bulk water removal |
Best Practices for Moisture Control in Compressed Air Systems
To maximize moisture removal efficiency, consider the following guidelines:
- System Design: Position aftercoolers and moisture separators as close to the compressor discharge as possible to reduce the air temperature and remove bulk condensate early.
- Regular Maintenance: Periodically inspect and replace desiccant media, clean dryer coils, and verify drain operation to maintain optimal performance.
- Monitor Dew Point: Use dew point sensors to continuously assess compressed air dryness and detect system faults.
- Avoid Pressure Drops: Design the system to minimize unnecessary pressure losses which can increase operational costs.
- Use Proper Drainage: Employ automatic drains on air receivers, filters, and dryers to prevent moisture accumulation.
- Environmental Considerations: Account for ambient temperature and humidity as they influence moisture load and dryer sizing.
Implementing these strategies ensures reliable moisture removal, protects equipment, and reduces downtime.
Methods for Removing Moisture from Compressed Air
Controlling moisture in compressed air systems is critical to maintaining equipment performance and preventing corrosion, freezing, or contamination. Several effective methods exist to remove moisture from compressed air, each suited to different applications and operating conditions.
Refrigerated Air Dryers
These dryers cool the compressed air to near freezing temperatures, causing water vapor to condense into liquid form. The condensed water is then separated and drained from the system. Refrigerated dryers are widely used due to their cost-effectiveness and ability to provide a consistent pressure dew point, typically around 3°C to 5°C (37°F to 41°F).
- Operate by heat exchange to lower air temperature
- Effective for general industrial applications
- Require regular maintenance of condensate drains
Desiccant Air Dryers
Desiccant dryers use hygroscopic materials that adsorb moisture from the compressed air. They are capable of achieving very low dew points, often below -40°C (-40°F), making them suitable for critical or sensitive applications such as instrumentation and paint spraying.
- Types include heatless, heated, and blower purge dryers
- Require periodic regeneration of the desiccant material
- Higher operational costs compared to refrigerated dryers
Membrane Air Dryers
Membrane dryers utilize semi-permeable membranes that allow water vapor to permeate through while retaining dry air. They are compact, have no moving parts, and are ideal for point-of-use drying or mobile applications.
- Provide dew points down to -40°C (-40°F)
- Low maintenance with no refrigerants or chemicals
- Limited flow capacity and higher initial cost
Coalescing Filters and Separators
These devices remove liquid water and aerosols from compressed air by coalescing small droplets into larger ones that can be drained away. While they do not reduce water vapor content, they are often used in conjunction with dryers to improve air quality.
- Effective for removing oil and liquid water droplets
- Require regular replacement of filter elements
- Improve downstream equipment reliability
Method | Typical Dew Point | Maintenance | Best Applications |
---|---|---|---|
Refrigerated Dryer | 3°C to 5°C (37°F to 41°F) | Moderate (condensate drain upkeep) | General industrial air systems |
Desiccant Dryer | Below -40°C (-40°F) | High (desiccant regeneration) | Critical processes, instrumentation |
Membrane Dryer | Down to -40°C (-40°F) | Low (membrane replacement) | Point-of-use, mobile applications |
Coalescing Filter | Does not reduce vapor moisture | Moderate (filter changes) | Removal of liquid water and aerosols |
Professional Insights on Removing Moisture From Compressed Air Systems
Dr. Emily Carter (Compressed Air Systems Engineer, Pneumatics Solutions Inc.) emphasizes that the most effective way to remove moisture from compressed air is through the use of refrigerated air dryers. These systems cool the air to condense water vapor, which can then be drained away, ensuring the air remains dry and preventing corrosion and damage to pneumatic equipment.
Michael Nguyen (Industrial Maintenance Specialist, AirTech Services) advises that incorporating desiccant dryers is critical in environments where ultra-dry air is necessary. Desiccant dryers absorb moisture chemically and are particularly useful in applications requiring dew points below freezing, thereby protecting sensitive instrumentation and manufacturing processes.
Sarah Lopez (Quality Control Manager, CleanAir Manufacturing) highlights the importance of proper filtration combined with moisture removal techniques. She notes that installing high-efficiency particulate filters alongside moisture separators can significantly reduce water content and contaminants, extending the lifespan of compressed air tools and improving overall system reliability.
Frequently Asked Questions (FAQs)
What causes moisture buildup in compressed air systems?
Moisture accumulates due to air cooling during compression, which causes water vapor to condense. Additionally, ambient humidity entering the system contributes to moisture presence.
What are the common methods to remove moisture from compressed air?
Common methods include using refrigerated air dryers, desiccant dryers, membrane dryers, and moisture separators or filters to effectively reduce water content.
How does a refrigerated air dryer work to remove moisture?
A refrigerated dryer cools compressed air to near-freezing temperatures, causing water vapor to condense into liquid, which is then separated and drained from the system.
When should a desiccant dryer be used instead of a refrigerated dryer?
Desiccant dryers are preferred for applications requiring very low dew points or in environments where air temperatures drop below freezing, as they absorb moisture chemically rather than relying on cooling.
Can moisture in compressed air damage equipment or processes?
Yes, moisture can cause corrosion, reduce equipment lifespan, contaminate products, and impair pneumatic tool performance, making moisture removal critical for system reliability.
How often should moisture removal equipment be maintained or inspected?
Maintenance frequency depends on usage and environment but generally involves regular inspection and servicing every 6 to 12 months to ensure optimal performance and prevent moisture-related issues.
Removing moisture from compressed air is essential to maintain the efficiency and longevity of pneumatic systems and equipment. Moisture in compressed air can lead to corrosion, contamination, and reduced performance, making it critical to implement effective drying methods. Common techniques include using refrigerated dryers, desiccant dryers, membrane dryers, and proper filtration systems, each suited to different operational requirements and environmental conditions.
Understanding the specific needs of your compressed air system is crucial when selecting a moisture removal method. Refrigerated dryers are typically used for general industrial applications due to their reliability and cost-effectiveness, while desiccant dryers are preferred for applications requiring extremely dry air. Membrane dryers offer a compact and energy-efficient solution for smaller-scale or portable systems. Additionally, regular maintenance and monitoring of the drying equipment ensure sustained performance and prevent moisture-related issues.
In summary, effective moisture removal from compressed air not only protects equipment and improves product quality but also reduces downtime and maintenance costs. Investing in the appropriate drying technology and maintaining it properly will result in a more reliable and efficient compressed air system, ultimately supporting operational excellence and longevity.
Author Profile
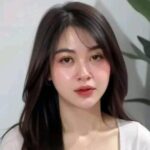
-
Tamika Rice is a lifestyle journalist and wellness researcher with a passion for honest, relatable storytelling. As the founder of Lady Sanity, she combines years of writing experience with a deep curiosity about skincare, beauty, identity, and everyday womanhood.
Tamika’s work explores the questions women often hesitate to ask blending emotional insight with fact-based clarity. Her goal is to make routines feel empowering, not overwhelming. Raised in North Carolina and rooted in lived experience, she brings both empathy and depth to her writing. Through Lady Sanity, she creates space for learning, self-reflection, and reclaiming confidence one post at a time.
Latest entries
- July 4, 2025Skincare & Acne CareCan I Use Body Sunscreen on My Face Safely?
- July 4, 2025Nail Care & BeautyHow Long Does a French Manicure Really Last?
- July 4, 2025Makeup & CosmeticsWhy Should You Never Go to the Cosmetics Counter Without Me?
- July 4, 2025Female Empowerment & IdentityHow Many Females Were On Board the Ship Ann?