How Is Makeup Foundation Made: What Ingredients and Processes Create Your Perfect Base?
Makeup foundation is a beauty staple that many reach for daily, serving as the perfect canvas to enhance and even out skin tone. But have you ever paused to wonder how this seemingly simple product is crafted? Behind every bottle or compact lies a fascinating blend of science, artistry, and innovation, designed to meet diverse skin needs and preferences. Understanding how makeup foundation is made offers a glimpse into the meticulous process that transforms raw ingredients into a flawless finish.
At its core, foundation is a complex formulation that balances pigments, oils, and other components to create a product that not only looks good but feels comfortable on the skin. The journey from concept to container involves careful selection of materials, precise mixing techniques, and rigorous testing to ensure quality and safety. Each step contributes to the foundation’s texture, coverage, and longevity, reflecting the expertise of cosmetic chemists and manufacturers.
Exploring the creation of makeup foundation reveals the intricate interplay between chemistry and creativity. Whether designed for light coverage or full concealment, foundations must harmonize performance with skin health, catering to a wide range of skin types and tones. This overview sets the stage for a deeper dive into the fascinating world behind one of the most essential products in the beauty industry.
Key Ingredients and Their Roles in Foundation Formulation
The formulation of makeup foundation involves a careful balance of various ingredients, each serving a specific function to ensure the product’s performance, texture, and skin compatibility. Understanding these components is essential for grasping how foundation is made and why it behaves the way it does.
Pigments are the primary ingredients responsible for the foundation’s color and coverage. These typically include:
- Titanium Dioxide and Iron Oxides: Commonly used for opacity and color matching.
- Mica: Adds a subtle shimmer or glow, contributing to a radiant finish.
- Ultramarines and Chromium Oxides: Used for specialized shades or undertones.
Emollients play a critical role in providing smooth application and skin hydration. These can be oils, esters, or silicones, such as:
- Dimethicone: A silicone that imparts a silky texture and forms a breathable barrier.
- Caprylic/Capric Triglyceride: A lightweight oil that moisturizes without heaviness.
Binders and film formers ensure that the foundation adheres well to the skin and maintains durability throughout wear. Commonly used binders include:
- Acrylates Copolymer: Creates a flexible film that resists smudging.
- Polyvinylpyrrolidone (PVP): Enhances adhesion and helps in water resistance.
Preservatives are necessary to inhibit microbial growth and prolong shelf life, given the product’s aqueous and oil-based composition. Examples include:
- Phenoxyethanol
- Parabens
- Ethylhexylglycerin
Additional ingredients such as thickeners, emulsifiers, and antioxidants are included to stabilize the formula, ensure uniform texture, and prevent oxidation of sensitive components.
Manufacturing Process of Liquid Foundation
The production of liquid foundation follows a systematic process that combines precise ingredient integration with strict quality controls to produce a consistent and safe product.
- Premixing of Pigments: Initially, pigments are dispersed in a liquid vehicle, often using a high-shear mixer. This step ensures uniform color distribution and prevents clumping.
- Emulsion Preparation: The oil and water phases are separately heated and mixed, typically around 70-80°C, to dissolve emulsifiers and enhance ingredient compatibility.
- Combining Phases: The pigment dispersion is slowly incorporated into the emulsion under continuous stirring to form a homogeneous mixture.
- Homogenization: The blend undergoes high-pressure homogenization to reduce particle size, improving texture, stability, and skin feel.
- Cooling: The foundation is gradually cooled to room temperature while maintaining agitation to prevent phase separation.
- Addition of Heat-Sensitive Ingredients: Fragrances, preservatives, and certain vitamins are added at this stage to preserve their efficacy.
- Filling and Packaging: The final product is transferred into sterilized containers, sealed, and labeled under cleanroom conditions.
Each stage is monitored for parameters such as pH, viscosity, color consistency, and microbial content to adhere to regulatory standards and consumer expectations.
Comparison of Foundation Types and Their Composition
Foundations come in various formulations tailored to different skin types and desired finishes. The following table summarizes the typical ingredient emphasis and characteristics across common foundation types:
Foundation Type | Key Ingredients | Texture | Finish | Ideal Skin Type |
---|---|---|---|---|
Liquid Foundation | Water, Silicone Oils, Pigments, Emulsifiers | Fluid to creamy | Natural to dewy | Normal to dry |
Powder Foundation | Talc, Mica, Pigments, Binding Agents | Powdery, lightweight | Matte | Oily to combination |
Cream Foundation | Emollients, Waxes, Pigments | Thick and rich | Full coverage, satin | Dry to mature |
Stick Foundation | Waxes, Oils, Pigments | Solid, blendable | Matte to satin | Normal to oily |
Mineral Foundation | Mineral Powders (Zinc Oxide, Titanium Dioxide), Mica | Loose or pressed powder | Natural, sheer | Sensitive, acne-prone |
This diversity in ingredients and formulation techniques allows manufacturers to cater to a wide spectrum of consumer needs, preferences, and skin concerns.
Quality Control and Safety Testing
Ensuring the safety and effectiveness of foundation products involves rigorous quality control protocols throughout the manufacturing lifecycle. Testing typically includes:
- Microbial Testing: To detect and eliminate contamination from bacteria, yeast, and molds.
- Stability Testing: Simulates various environmental conditions (temperature, humidity, light exposure) to verify product integrity over time.
- Patch Testing: Assesses potential skin irritation or allergic reactions on human volunteers or in vitro models.
- Color Consistency: Uses spectrophotometric analysis to confirm uniform shade across batches.
- Viscosity and Texture Assessment: Employs rheometers to measure flow characteristics ensuring ease of application.
Manufacturers comply with regional and international regulatory requirements such as the
Ingredients and Raw Materials Used in Makeup Foundation
Makeup foundation formulations are complex and designed to meet specific performance criteria such as coverage, texture, longevity, and skin compatibility. The primary categories of raw materials used in foundation production include pigments, binders, emollients, solvents, preservatives, and additives. Each plays a critical role in achieving the desired product characteristics.
- Pigments: These provide color and coverage. Common pigments include titanium dioxide and zinc oxide (for opacity and sun protection), iron oxides (for skin tone matching), and ultramarines.
- Binders: These help particles adhere to each other and to the skin, ensuring uniform application and durability. Examples include silicones (e.g., dimethicone), acrylic polymers, and natural gums.
- Emollients: Oils and fats that provide smoothness, hydration, and a pleasant skin feel. Examples include mineral oils, plant-derived oils (jojoba, almond), and esters.
- Solvents: Liquids that dissolve other ingredients and facilitate mixing. Water and alcohols are commonly used depending on the foundation type (liquid, cream, powder).
- Preservatives: Prevent microbial growth to ensure product safety and shelf life. Parabens, phenoxyethanol, and ethylhexylglycerin are typical preservatives.
- Additives: These enhance performance or aesthetics, such as thickeners (e.g., xanthan gum), UV filters, antioxidants, fragrance, and skin-conditioning agents.
Manufacturing Process of Makeup Foundation
The production of makeup foundation involves precise formulation and controlled processing steps to ensure consistent quality and efficacy. The process differs somewhat depending on the foundation type—liquid, cream, powder, or mousse—but generally follows these core stages:
Step | Description | Purpose |
---|---|---|
Raw Material Preparation | Weighing, sifting, and pre-mixing of pigments and powders. | Ensure accurate dosing and homogenous pigment dispersion. |
Dispersion | High-speed mixing or milling to evenly distribute pigments in solvents or oils. | Prevent clumping and achieve uniform color and texture. |
Emulsification (for liquid/cream foundations) | Combining oil and water phases using homogenizers. | Create stable emulsions that do not separate over time. |
Incorporation of Additives | Adding preservatives, thickeners, fragrances, and active ingredients. | Enhance product stability, safety, and sensory attributes. |
Filling and Packaging | Filling the foundation into bottles, tubes, or compacts under hygienic conditions. | Protect product integrity and provide consumer-friendly formats. |
Quality Control | Testing for color accuracy, viscosity, microbial contamination, and stability. | Ensure the product meets specifications and regulatory requirements. |
Types of Foundation Formulations and Their Production Variations
Makeup foundation comes in several formulations, each requiring specific manufacturing adjustments to optimize performance and application:
- Liquid Foundation: Typically an oil-in-water or water-in-oil emulsion. Requires precise emulsification and control of viscosity to ensure smooth application and long wear.
- Cream Foundation: Contains a higher concentration of oils and waxes, often produced using heat to melt and blend thickening agents, followed by slow cooling to set the texture.
- Powder Foundation: Made by blending pigments with talc, mica, and binding powders. Production involves dry mixing and sometimes compression into compacts rather than emulsification.
- Mousse Foundation: Incorporates air into a creamy base using whipping processes, requiring stabilizers to maintain the light, airy texture.
Quality and Safety Considerations in Foundation Manufacture
Ensuring the safety, consistency, and performance of makeup foundation involves stringent quality control measures throughout the manufacturing process. Key considerations include:
- Microbial Control: Use of preservatives and aseptic processing to prevent contamination.
- Allergen and Irritant Testing: Screening ingredients and final products to minimize skin irritation and allergic reactions.
- Stability Testing: Assessing color, texture, and emulsion stability under varying temperature and light conditions.
- Regulatory Compliance: Adherence to cosmetic regulations such as FDA (U.S.), EU Cosmetics Regulation, and others regarding ingredient safety and labeling.
- Batch-to-Batch Consistency: Use of standardized raw materials and precise manufacturing protocols to ensure uniform product quality.
Expert Perspectives on How Makeup Foundation Is Made
Dr. Elena Martinez (Cosmetic Chemist, BeautyScience Labs). The manufacturing of makeup foundation involves a precise blend of pigments, emollients, and binders to achieve a smooth, consistent texture. The process starts with selecting high-quality raw materials, which are then milled and mixed under controlled conditions to ensure uniform particle size and color distribution. Stability testing follows to guarantee the product maintains its integrity over time.
James O’Connor (Formulation Specialist, Dermaceutical Innovations). Foundation creation requires balancing aesthetics with skin compatibility. Ingredients such as silicones and oils are combined with mineral pigments to provide coverage and a natural finish. The formulation process also includes adjusting pH levels and incorporating preservatives to enhance safety and longevity, all while adhering to regulatory standards.
Priya Singh (Quality Control Manager, Luxe Cosmetics). Quality assurance is critical in foundation production. Each batch undergoes rigorous testing for texture, shade accuracy, and microbial contamination. The manufacturing environment is strictly monitored to prevent contamination, and continuous sampling ensures that every product delivered to consumers meets the highest standards of performance and safety.
Frequently Asked Questions (FAQs)
What are the primary ingredients used in makeup foundation?
Makeup foundation typically contains pigments for color, emollients for smooth application, binders to hold ingredients together, preservatives to prevent microbial growth, and sometimes sunscreen agents for UV protection.
How is the pigment in foundation created and incorporated?
Pigments are finely milled mineral or synthetic powders that provide color and coverage. They are carefully blended with oils and binders to ensure even distribution and a natural finish.
What role do emollients play in foundation formulation?
Emollients provide moisture and improve the texture, allowing the foundation to spread smoothly over the skin and enhance wearability.
How is the consistency of foundation controlled during manufacturing?
Manufacturers adjust the ratio of liquids to powders and use thickeners or stabilizers to achieve the desired viscosity, whether liquid, cream, or powder form.
Are there different manufacturing processes for various foundation types?
Yes. Liquid foundations often undergo mixing and homogenization, cream foundations require emulsification, and powder foundations involve milling and pressing of pigments and powders.
How is quality and safety ensured in foundation production?
Stringent quality control measures include ingredient testing, microbial analysis, stability testing, and compliance with regulatory standards to ensure product safety and efficacy.
Makeup foundation is meticulously formulated through a combination of pigments, emollients, binders, and preservatives that work together to create a smooth, even complexion. The process begins with selecting high-quality raw materials, including colorants that match various skin tones, and base ingredients such as oils, water, and silicones that determine the texture and finish. These components are carefully blended and milled to achieve a consistent and stable product that adheres well to the skin.
Advanced manufacturing techniques ensure that foundations meet safety and performance standards, including thorough testing for skin compatibility and durability. The formulation can vary widely depending on the desired type of foundation—whether liquid, cream, powder, or stick—each requiring specific ingredient balances and processing methods. Additionally, modern foundations often incorporate skincare benefits, such as hydration, sun protection, and anti-aging properties, reflecting the evolving demands of consumers.
In summary, the creation of makeup foundation is a complex and highly controlled process that balances aesthetic appeal with functional performance. Understanding the key ingredients and manufacturing steps provides valuable insight into how foundations deliver both coverage and skin care benefits. This knowledge underscores the importance of formulation expertise in producing high-quality makeup products that cater to diverse skin types and preferences.
Author Profile
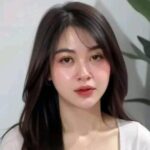
-
Tamika Rice is a lifestyle journalist and wellness researcher with a passion for honest, relatable storytelling. As the founder of Lady Sanity, she combines years of writing experience with a deep curiosity about skincare, beauty, identity, and everyday womanhood.
Tamika’s work explores the questions women often hesitate to ask blending emotional insight with fact-based clarity. Her goal is to make routines feel empowering, not overwhelming. Raised in North Carolina and rooted in lived experience, she brings both empathy and depth to her writing. Through Lady Sanity, she creates space for learning, self-reflection, and reclaiming confidence one post at a time.
Latest entries
- July 4, 2025Skincare & Acne CareCan I Use Body Sunscreen on My Face Safely?
- July 4, 2025Nail Care & BeautyHow Long Does a French Manicure Really Last?
- July 4, 2025Makeup & CosmeticsWhy Should You Never Go to the Cosmetics Counter Without Me?
- July 4, 2025Female Empowerment & IdentityHow Many Females Were On Board the Ship Ann?